[EN-US] Marketing Materials Page - GORE-TEX CROSSTECH® PYRAD® stretch products - EMS - Downloadable
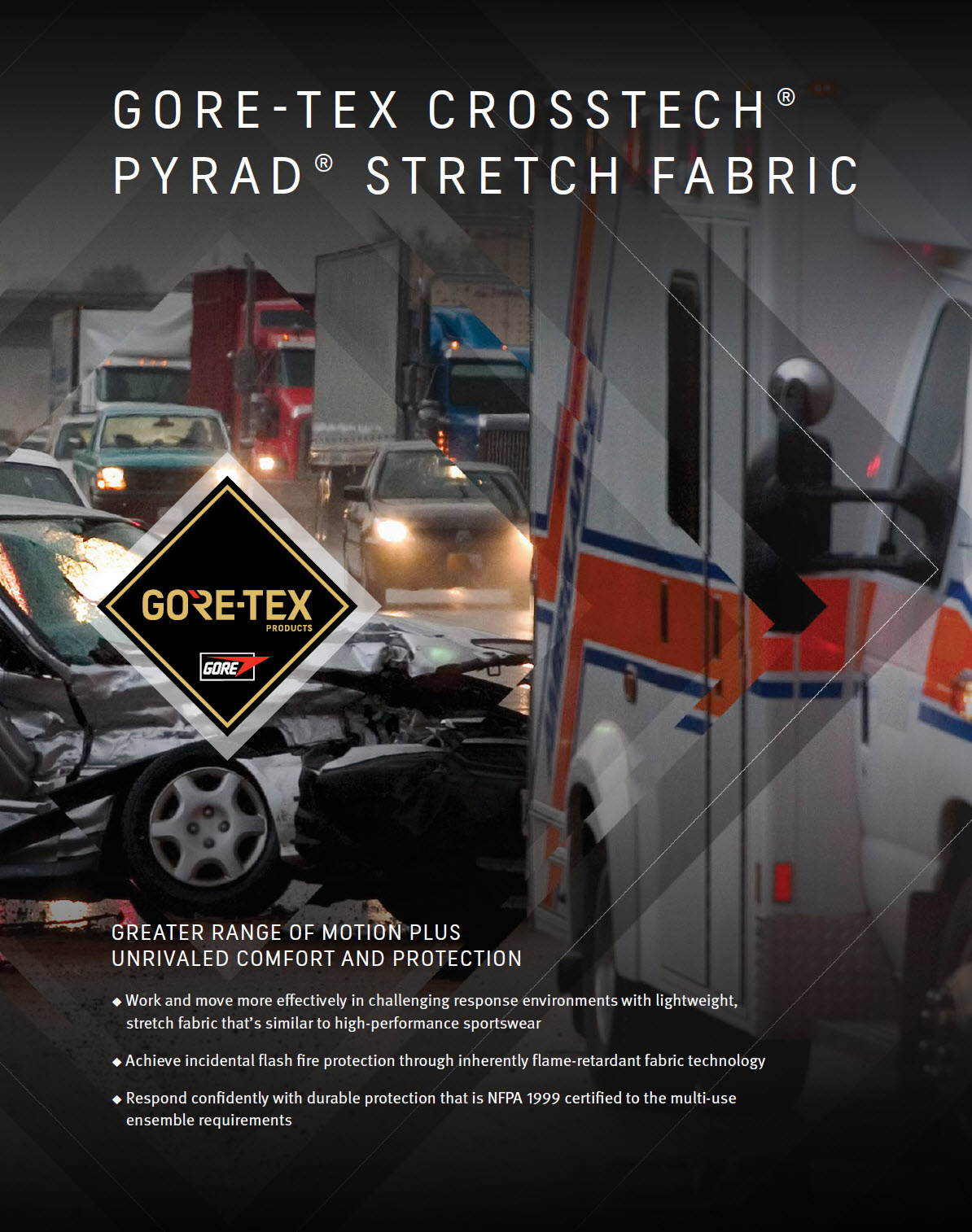
Issues related to firefighter safety and protection are extremely important to W. L. Gore & Associates. For 40 years, Gore has been continuously researching, developing and manufacturing a portfolio of products for firefighters — to offer the best range of products we can, to enable firefighters to do their jobs safely and effectively.
As a material science company, Gore carefully selects materials most appropriate for the unique specifications of each product and end use application.
We follow the developing science, do our own extensive internal testing and invest in independent research to develop high performing products that meet or exceed the applicable performance and safety standards in the geographies where our products are sold. We are committed to innovation and seek continuous improvement in our products to meet the needs of firefighters and comply with the appropriate industry standards.
Structural firefighting apparel demands materials with properties that provide the highest level of thermal, physical and biological protection to the men and women working in harsh and often dangerous conditions. For example, GORE® moisture barriers, a component of structural firefighting turnout gear, are fabric laminates composed of flame resistant (FR) textiles, adhesives, coatings, and a thin waterproof breathable membrane. GORE® moisture barriers for turnout gear are OEKO-TEX® Standard 100 certified, an international safety standard for textile products.
POLYTETRAFLUOROETHYLENE (PTFE)
Gore uses a fluoropolymer, ePTFE (an expanded form of PTFE) for the thin waterproof and breathable membranes at the heart of all of our GORE® moisture barrier products for the firefighting industry.
Fluoropolymers, like PTFE, are valuable materials with unique properties that enable high performing products across a range of industries and end uses. For more than 60 years, Gore has applied its deep understanding and expertise in working with PTFE to develop products of high societal value ranging from enabling technology for industrial filtration, to communication systems used onboard aircraft and in space exploration, to implantable medical devices that save and improve lives.
The chemical and physical properties of PTFE make it ideal for use in demanding applications with harsh conditions such as structural firefighting. For example, PTFE is insoluble in water, durable, and extremely stable — enabling it to withstand exposure to a wide range of corrosive substances and maintain its performance in extreme temperatures. To Gore’s knowledge, PTFE-based moisture barriers are presently the only available technology for turnout jackets and pants that meets the current edition of NFPA 1971: Standard on Protective Ensembles for Structural Fire Fighting and Proximity Fire Fighting.
PER AND POLY FLUOROALKYL SUBSTANCES (PFAS)
PFAS stands for Per- and Polyfluoroalkyl substances and describes a wide range of chemistries with very different properties and uses. Because there are clear and important distinctions between the more than 4,700 materials often referred to as PFAS, it is a very complex topic. Therefore, when communicating about PFAS, we believe it is important to be specific about the particular chemistries or type of PFAS being discussed.
There are significant distinctions between the chemical and physical properties of fluoropolymers like PTFE and other materials most often associated with the term PFAS. PTFE does meet the very broad definition of the term despite the important distinctions. Often, however, when people are using the term PFAS, they are referring to non-polymer PFAS such as PFOA.
Historically, residual PFOA could be measured in some of our fabrics at trace levels, though the products were safe for their intended use. In alignment with the EPA PFOA Stewardship program, Gore worked closely with its suppliers to remove PFOA from its global fabrics supply chain. This was successfully completed in 2013.
To evaluate potential exposures and associated risks of cancer for firefighters associated with any traces of these small non-polymer PFAS that may remain in our products, Gore has conducted exposure assessments on our moisture barriers with both our historic and current moisture barrier products. Gore conducted these assessments in accordance with EPA-approved methodologies, incorporating publicly available data and relevant Gore product information. Exposures and risks were calculated using a series of standard equations for multiple potential routes of exposure, including skin contact, hand-to-mouth contact, ingestion of dust, and inhalation of particulates. The assessments determined that even if the product is worn over an entire career of a firefighter, the highest potential level of non-polymer PFAS in Gore’s moisture barriers was well below the levels of exposure that were determined to be safe. These assessments are in addition to the moisture barrier products meeting the criteria for OEKO-TEX® Standard 100 certification.
DURABLE WATER AND OIL REPELLANT TREATMENTS
Durable water and oil repellent treatments (DWR) are often applied to Gore’s moisture barrier products. These treatments provide important water and oil repellency for the laminate to help keep water and other contaminates from soaking into the barrier materials, and also help maintain the performance of the waterproof membrane over time. High-performing durable water repellency treatments can also reduce the burden associated with wet fabrics, which can also potentially impact performance.
The high-performing DWR treatments that Gore currently uses in its moisture barrier products are based on a type of PFAS known as short-chain side chain fluorinated polymers, which may contain trace residuals of non-polymer PFAS. We recognize that questions are being asked about these trace non-polymer PFAS residuals found in the DWR treatments. These trace non-polymer PFAS were included in our exposure assessments. Gore actively monitors the science regarding DWR chemistries and is actively exploring new durable water and oil repellency treatments that utilize different chemistries than the current side chain fluorinated polymer treatments. Our goal is to offer our customers even more choices as we identify alternative technology that can be used without making significant compromises in product performance.
For more than 20 years, Gore has also offered a moisture barrier that does not contain water and oil repellency treatments, the GORE® RT7100 moisture barrier. This product is compliant to NFPA 1971, yet the absence of a DWR treatment can make it more susceptible to picking up water and oil in use relative to other GORE® moisture barriers.
GOING FORWARD
Gore is unwavering in our commitment to the safety of the men and women who depend on our moisture barrier products when working in harsh and often dangerous conditions. In response to the requests by our customers and firefighters to have an even wider range of technology choices available, Gore plans to offer an additional product that does not contain DWR treatments. It is important to recognize, however, the potential for performance tradeoffs over the life of those products.
Gore will continue to evaluate the developing science and information and apply that knowledge to our product development efforts to inform our material choices and ensure that our products offer an acceptable combination of performance, breathability, durability, and protection. Our research and development efforts also include tapping into Gore’s extensive material science expertise and network of resources to identify potential additional technologies that could possibly meet the NFPA 1971 Standard. We are working hard to address these complex challenges.
As one of the busiest departments in the country, St. Petersburg Fire Rescue in Florida has committed resources to elevate the protection of their firefighters at the fire scene. For two years the department’s Safety and Training Division has been researching health and wellness issues as the industry continues to publish studies about fireground contaminants. It has focused its first efforts on upgrading fireground protocols and turnout gear, specifically related to hoods.
A member of the Safety and Training Division, Lieutenant Robert Neuberger, says,
“Several firefighters in our area have needed aggressive treatment for neck and throat cancer, so this has been an important issue for our department. Our unit decided we needed to upgrade the department-issued hoods to NFPA-certified particulate hoods to provide better protection against fireground particulates.”
The group evaluated various particulate hoods on the market and set the requirements for a hood that provided the highest level of certified protection after being washed repeatedly using the NFPA laundering protocols.
The Safety and Training Division ran a wear trial during which firefighters from the two busiest stations evaluated the hood for more than 60 hours, which included responding to structural fire and hazmat calls. They had two important reasons for the wear trial. First, they wanted to ensure that the hood performed well in real fireground conditions. Second, and just as important, they wanted to make sure that the firefighters liked the particulate hood; the firefighters that evaluated the new hoods have been in the service for many years, so this would be a change for them. According to Neuberger, the firefighters’ feedback was very positive, saying,
“The GORE® Particulate Hood was comfortable, and it provided better protection. It fit around the neck and the longer length stayed tucked in. They really liked the combination of the inspection opening and the red stitching that was only on the outside. The stitching helps them be sure they have the right side out after using the inspection opening to visually check the particulate-blocking barrier for cuts, tears, or holes.”
So, based on this feedback, St. Petersburg purchased 400 GORE® Particulate Hoods.
The Safety and Training Division talked with their MES dealer, John Schmidt, about decontamination protocols. As a retired firefighter, John had been doing his own research, and he had been developing protocols at his department before he retired. St. Petersburg has just ordered an additional 400 hoods so that each firefighter can swap out his or her hood during rehab at the fire scene. Neuberger explains,
“It doesn’t make sense for us to stress wearing a clean hood for every call if they don a filthy hood when they return to the scene after rehab. Once we receive the additional hoods, our protocol will require all firefighters to don a fresh hood after rehab to help avoid contaminating their neck and face if they were to pull on a dirty hood.”
When asked about dealing with the increased costs of this program, Lieutenant Neuberger said the Safety and Training Division faced this potential issue directly.
“We justified the investment by researching the total cost of our health and wellness programs, including health insurance and the impact of sick days. We also considered the importance of the morale of our firefighters. If they know we are looking out for their health and welfare by providing the best possible gear, then that has a positive effect on their morale. This can go a long way when they are hearing a lot about the health issues of fireground particulates.”
For more information about the St. Petersburg program, contact Lt. Robert Neuberger at Robert.Neuberger@stpete.org.
About St. Petersburg Fire Rescue
With a force of 342 firefighters and paramedics, St. Petersburg Fire Rescue, Florida, has 32 pieces of firefighting apparatus, 14 fire stations, and an administrative building. The department provides specialized life safety services by staffing three specialty teams. The technical rescue team responds to elevated, below-grade, confined-space, and structural collapse rescues. The hazardous materials team handles spills and releases of toxic substances, liquids, or gases countywide. Staffed by certified rescue divers, the dive and marine rescue team responds to victim emergencies on St. Petersburg's many waterways. St. Petersburg Fire Rescue protects the lives and property of over 260,000 residents and responds to over 63,958 emergency incidents annually.
Media Contact
Lt. Steve Lawrence
St. Petersburg Fire Rescue
Steven.Lawrence@stpete.org
727.893.7709
# # #
ELKTON, Md. (May 29, 2018) – W. L. Gore & Associates’ Protective Fabrics Division has expanded its line of certified products for emergency responders with the addition of the Ruggedized Class 3 suit made of GORE® CHEMPAK® selectively permeable fabric. Manufactured and distributed by Blauer® Manufacturing Company, Inc., the Ruggedized Class 3 suit is certified to NFPA1994, Class 3R and NFPA 1992 Standards (2018 Edition). The suit’s ruggedized construction makes it ideal for extended CBRN responses that include tactical entry or search & rescue missions for several reasons.
First, the GORE® CHEMPAK® selective permeable fabric is engineered to deliver extremely durable protection against potential exposure to liquid and vapor chemicals, biological, and radiological particulates, blood and body fluids, and emerging pharmaceuticals such as fentanyl — even after exposure to field contaminants such as seawater, sweat, and hydraulic fluid.
Second, the form-fitting garment, with reinforced padding at critical stress points for a greater level of cut and puncture resistance, is designed to enable the responder to move more easily and effectively throughout hazardous surroundings, confined spaces, and rubble piles.
Third, the highly breathable GORE® CHEMPAK® selectively permeable fabric enables the responder to stay actively involved in the mission significantly longer than an impermeable suit does. While maintaining a minimum of four hours of permeation protection, Gore’s barrier enables sweat vapor to escape through the suit, which helps reduce heat stress.
And finally, the NFPA certifications and AEL/SEL qualifications of the Ruggedized Class 3 suit make it eligible for grant funding.
According to Jason Horowitz, Gore’s North American Chem-Bio product manager, their team works closely with end users to identify their needs when developing a new product. CBRN responders had described the challenges of needing protection in harsh surroundings combined with the capability of operating in temperature and humidity extremes. He explained, “The new garment needed to be durable enough to withstand rigorous use associated with tactical entry or search and rescue operations, providing a greater level of cut and puncture resistance than the current Class 3 ensembles. It also needed to provide increased visibility, range of motion, and dexterity, while optimizing the integration of helmets and ballistic vests. We’re really excited about offering this new level of durability in a certified Class 3R garment.”
For more information, visit GoreChempak.com.
About Gore Fabrics
Gore Fabrics Division revolutionized the outerwear industry with waterproof, breathable
GORE-TEX fabric 40 years ago and remains a leading innovator of performance apparel. Gore fabrics products provide comfort and protection in challenging environments and in everyday life, enabling wearers to safely and confidently achieve and experience more. From hiking in downpours to military operations and fighting fires, Gore’s deep understanding of consumer and industry needs drives development of products with meaningful performance advantages. GoreProtectiveFabrics.com
About Gore
W. L. Gore & Associates is a global materials science company dedicated to transforming industries and improving lives. Founded in 1958, Gore has built a reputation for solving complex technical challenges in the most demanding environments — from revolutionizing the outerwear industry with GORE-TEX fabric to creating medical devices that improve and save lives to enabling new levels of performance in the aerospace, pharmaceutical and mobile electronics markets, among other industries. The company is also known for its strong, team oriented culture and continued recognition from the Great Place to Work® Institute. Headquartered in Newark, Del., Gore employs approximately 9,500 Associates and generates annual revenues that exceed $3 billion. www.gore.com
# # #
Media Contact
Marie Y. Smith
Smith Consulting
Wilmington, DE 19808
Telephone: +1 302.994.0117
Email: mysmith115@comcast.net