or in the words of a navy seal testing gore-tex gear "this is good sh**"
A conversation with former Navy SEAL Master Chief Scott Williams and former Gore Associate Wayne Von Stetton.
The legacy of W.L. Gore & Associates (Gore) providing protective and comfortable clothing systems to the US Army goes back more than four decades. Already in 1978, the "Rainwear Division" of Gore first provided a sample of GORE-TEX laminate to the US Army Lab at Natick (currently known as DEVCOM or the Combat Capabilities Development Command — Soldier Center) but it did not gain much traction. Four years later, Wayne Von Stetten joined Gore and, early in his career, founder and CEO Bill Gore, came to Wayne and asked him to explore the military market in the US. At the time, Bill's grandson was serving in the military, and Bill believed they could benefit from improved clothing.
Figur
e 1: October 1983, a group of 4 Gore Associates left from the Joint Expeditionary Base - Little Creek, VA to Goose Bay, Canada, for an extensive product testing. Source: Wayne von Stetten.
soldiers purchased forest green mountain parka
No wonder as at that time most of the cold weather clothing the US Army was using, went back to the technology of what was worn in the Korean War, and they hadn't made many advances since then. In the early 1980's, many of the troops and warfighters were buying consumer gear from Marmot — the Mountain Parka in forest green color — or from companies like The North Face or Eddie Bauer with their own money, as it was assumed that the government would not pay the high prices for good weather protective gear. "The story was that the U.S. suffered more casualties to the elements and cold weather than they had lost in battle during the Korean War - not sure if that's true or not, but that's what was being said at the time", says Wayne.
1985/86 ecwcs generation i — waterproof and breathable but static
"Another event that gave GORE-TEX products a boost was the Falkland Island War between the UK and Argentina over British dependent territories in the South Atlantic. Argentina invaded and occupied the Falkland Islands and the British defended and ultimately regained their territory", reports Wayne. "Many of the Royal Marines, SAS, and British Army were wearing or testing GORE-TEX products at the time and gave it a huge endorsement over their conventional gear", he continues.
The British troops were raving about the performance of the GORE-TEX gear in the field. They also attested to the increased efficiency and focus of the troops thanks to their level of comfort. In 1983, the U.S. Government agreed to fund a 3-year development program code-named ECWCS (Extended Cold-Weather Clothing System) and a year later, three different service branches tested GORE-TEX sample products: the USMC 3rd MEF (Marine Expeditionary Force) at the Marine Corps Mountain Warfare Training Center, Pick Meadows, Bridgeport, CA; the NSW SEAL teams 2, 4, 6 (East Coast); and the US Army 10th Mountain Group — Ft. Drum, NY and in Italy. Scott Williams, former Navy SEAL Team 2 Master Chief, was an earlier tester for the GORE-TEX gear.
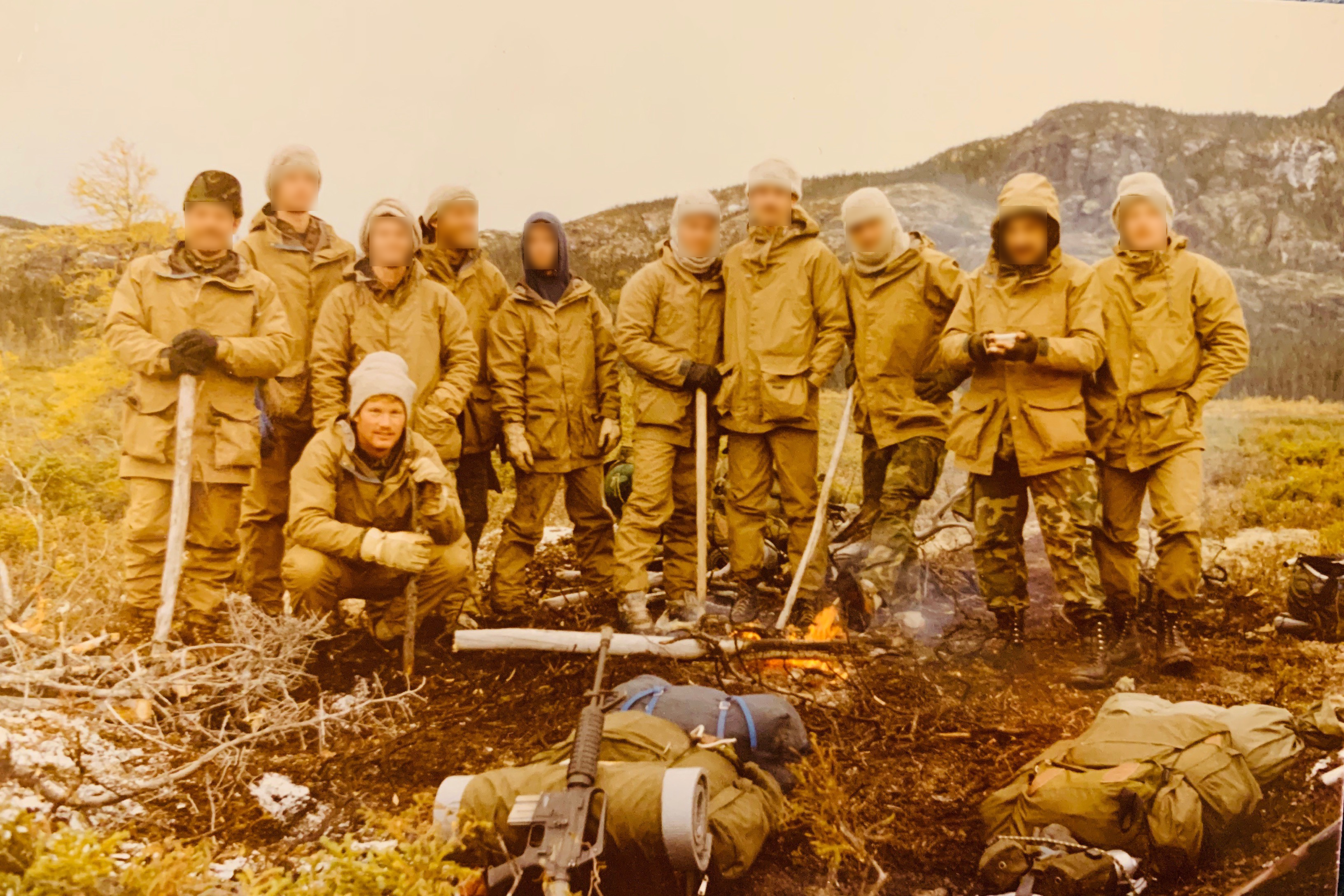
Figure 2: Scott Williams, former Navy SEAL Team 2 Master Chief and Navy SEALs testing GORE-TEX Products in the Meely Mountains, Goose Bay, Labrador, Newfoundland. Source: Scott Williams.
In the winter of 1984, trials in Alaska and at Fort Ethan Allen in Vermont were successful, achieving an operational capability at -40 degrees Fahrenheit. The next year one thousand U.S. marines participated in a NATO European invasion exercise in Norway without a single cold weather casualty, a first for the U.S. Marine Corps. The positive test feedback from Marines, SEALS and Mountain groups as well as the experience made by the British Armed Forces led to the initial order for about 10,0000 yards to develop the first ECWCS Parka in 1985/1986 together with a military garment contractor, Tennessee Apparel.
Figure 3: ECWCS Gen I - waterproof-breathable GORE-TEX garments. Source: Gore Heritage & Archives Collection
Mid 1990s - ecwcs generation ii - waterproof by design
Then in 1988, the first major order for general use resulted in 250,000 sets and ECWCS became the uniform of choice. The system became so popular that the demand exceeded the Army's initial five fielding plan, so the government allowed Gore to GORE-TEX ECWCS gear through the Military Exchange Stores. In the same year, Gore Associates were challenged to test the gear themselves. So, a team of military sales Associates from the UK, Germany, Sweden, France and Italy took a trip north of the arctic circle in Sweden and spent three days and nights marching and sleeping outside, putting the products to the test limits. "That allowed us to test the product to prove 'We've used it, we tested it'. When talking to military personnel, we were able to say that we tested the gear, and not repeat what we read in a book or letter", says Wayne.
In 1991 at the AUSA trade show, Army Chief of Staff, General Gordon Sullivan, stopped by Gore's booth and spoke with a young Product Specialist, Terri Kelly (who, by the way, became CEO of Gore in the mid-2000s) about GORE-TEX parkas leaking. Just a couple of years later, winter of 1993, Scott Williams was sitting in a ski lift in Alaska along with his Commanding officer. Both wearing GORE-TEX gear, but only one — Scott — was comfortable and dry as he was wearing a Marmot Alpinist jacket whereas his skipper's gear was not, and the reason was a poorly designed military garment at the time. "I realized the importance of design. Even if you have the best material in the world, it needs to be built right, and so we worked with the outdoor company Patagonia to design PCU Level 6 so it was storm certified", confirmed Scott Williams.
"The feedback from General Sullivan and experience made by the SEAL team, led to the development of garments that were also waterproof by design/fit-for-use with flaps over and under the zipper and other leakage areas. Eventually, it led to a new improved design that became a Generation II of ECWCS in the early mid-1990s", Wayne explains.
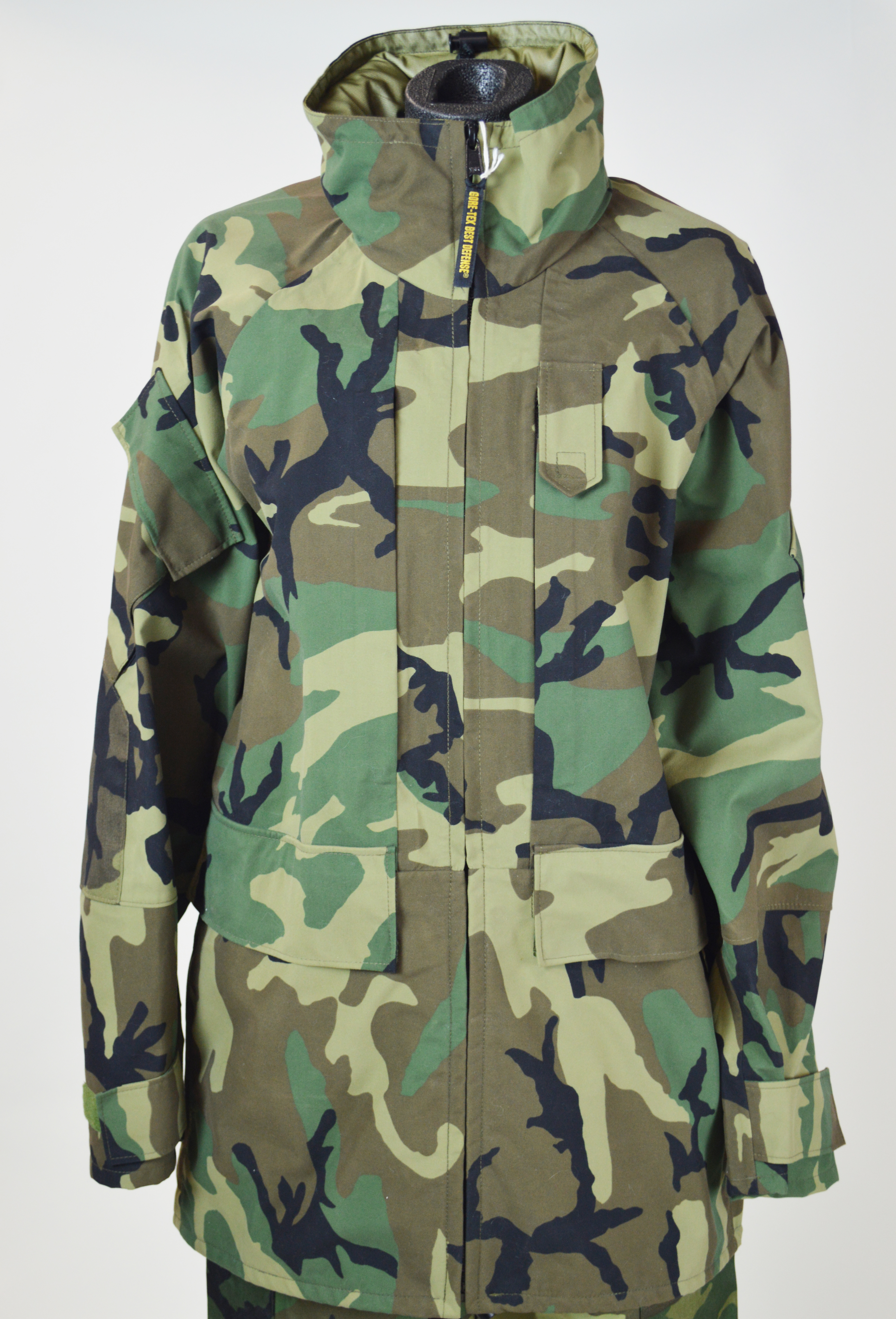
Figure 4: ECWCS Gen II - GORE-TEX garments with improved design. Source: Gore Heritage & Archives Collection
A key requirement for developing the second generation of ECWCS was to lighten the load of the soldiers, allowing the to get four hours of uninterrupted sleep without getting wet. From the mid-90s onwards, full special operations acted with rapid movements and rapid strike activities. Special Operation warfare concentrated on fast movement and rapid mission achievement. Being cold or wet can be a major distraction so staying dry and comfortable allowed SOF Operators to focus on the mission at hand "The command was 'get in and out fast'", explains Wayne. He continues: "From 1982-2003, Gore focused on expansion into other markets - firefighting, law enforcement, workwear, etc. - but there was not a lot of new product development in the military but then Gore stood up and developed new, higher performing and lighter material."
2003/2004 ecwcs generation iii - introducing a multi-layer system
The third generation ECWCS was developed as a multi-layered system. Initially, the SOCOM Program Office at NATICK started developing a multi-layered system based on products used in outdoor adventure sports (Alpinist, Skiing, Hunting, etc.). The challenge was to develop a multi-layer system that could be interchangeable based on the weather conditions and work activity level. The idea was to keep the body dry both from the outside elements but also on the skin. They required wicking base layers and breathable outer layers. SOCOM developed the Protective Combat Uniform (PCU) based input from outdoor enthusiasts like Mark Twight and high-end consumer outerwear brands (Patagonia, TNF, Marmot, etc.). Level 6 on the PCU was a cold, wet weather layer which incorporated a 2-Layer GORE-TEX laminate. In 2004, based on the PCU, the US Army was hesitant to update to a 3rd generation due to cost but, there were some instrumental stakeholders that helped push through the need for correct design. The Army quickly adopted the concept and developed a very similar 7-layer system called GEN III ECWCS but in Army camouflage and some other slight modifications.
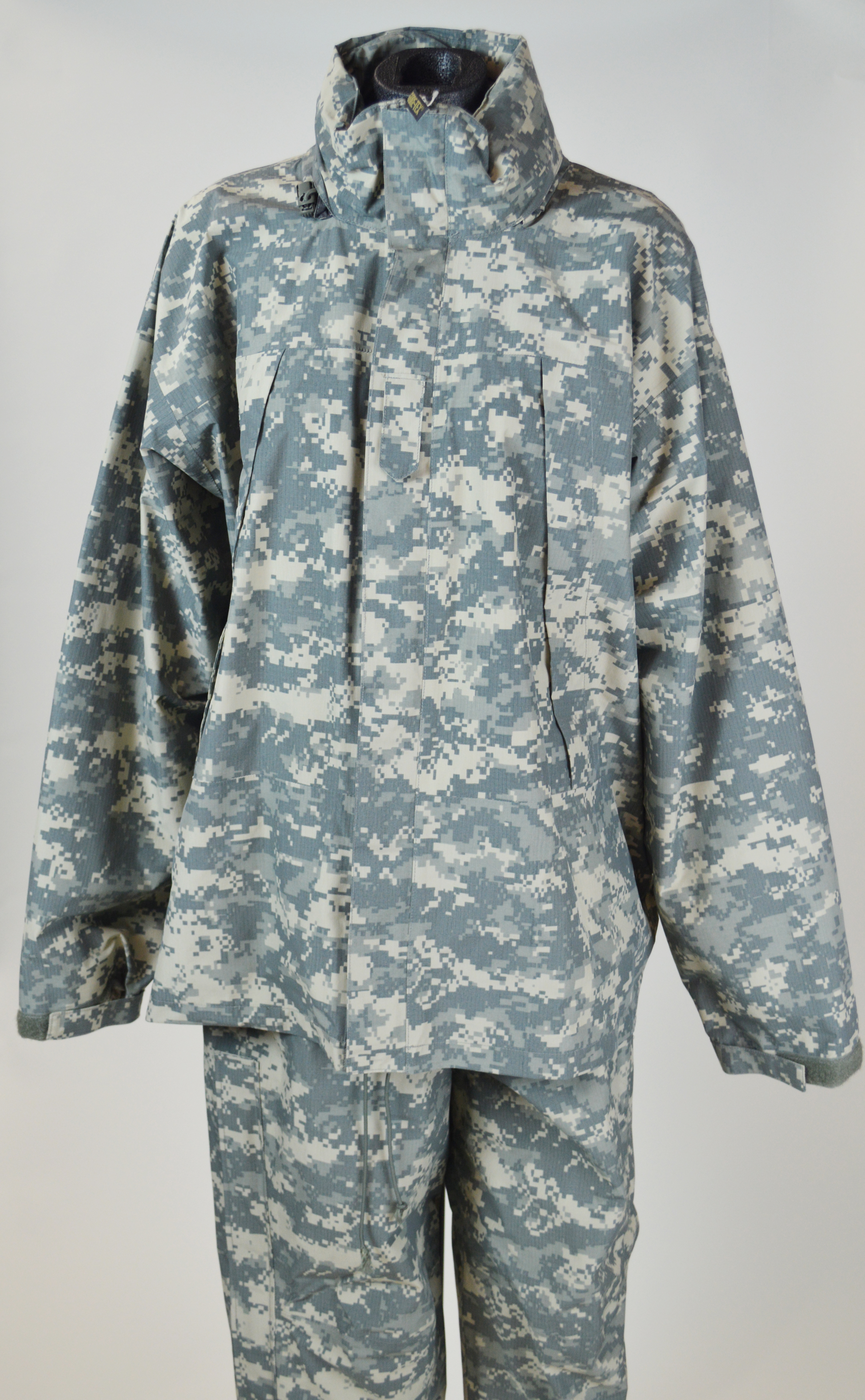
Figure 5: ECWCS Gen III - waterproof-breathable GORE-TEX Layer 6 of multi-layer system, currently used by US Army. Source: Gore Heritage & Archive Collection.
ECWCS Generation IV
After providing protection and comfort through GORE-TEX defense products to the US Army, US Air Force, US Navy, US Marines and SOCOM for more than 40 years, it is now time for the next generation of ECWCS taking into account all the learnings, feedback and input from decades of hard innovative work, both in the labs and in the field. At this year's AUSA show, Gore will be presenting system ideas and innovative technologies around the next generation All Weather Clothing System.
"This is good sh.."
Looking back all those years, Scott and Wayne summarize their experience with GORE-TEX products. Scott: "Even though you can have the best materials in the world, it still has to be built correctly, that is one of my main takeaways in working with Gore." Wayne adds, "Ultimately, we were able to reduce the number of people who died from environmental casualties. ECWCS gave greater capabilities to operate for longer. Soldiers referred to GORE-TEX as a 'force multiplier' which means making 10 soldiers worth 15, as they were able to carry more, and had better protection for their hands and feet as well (the use of GORE-TEX footwear and gloves grew significantly in those years). It's about extending the range, how long they can go and operate." I asked Wayne if he remembers a quote from a user when testing the GORE-TEX garments. "During an extensive test in cold and wet environment, I asked a solder 'How do you like GORE-TEX gear?' and his response was 'This is good sh**!", remembers Wayne.
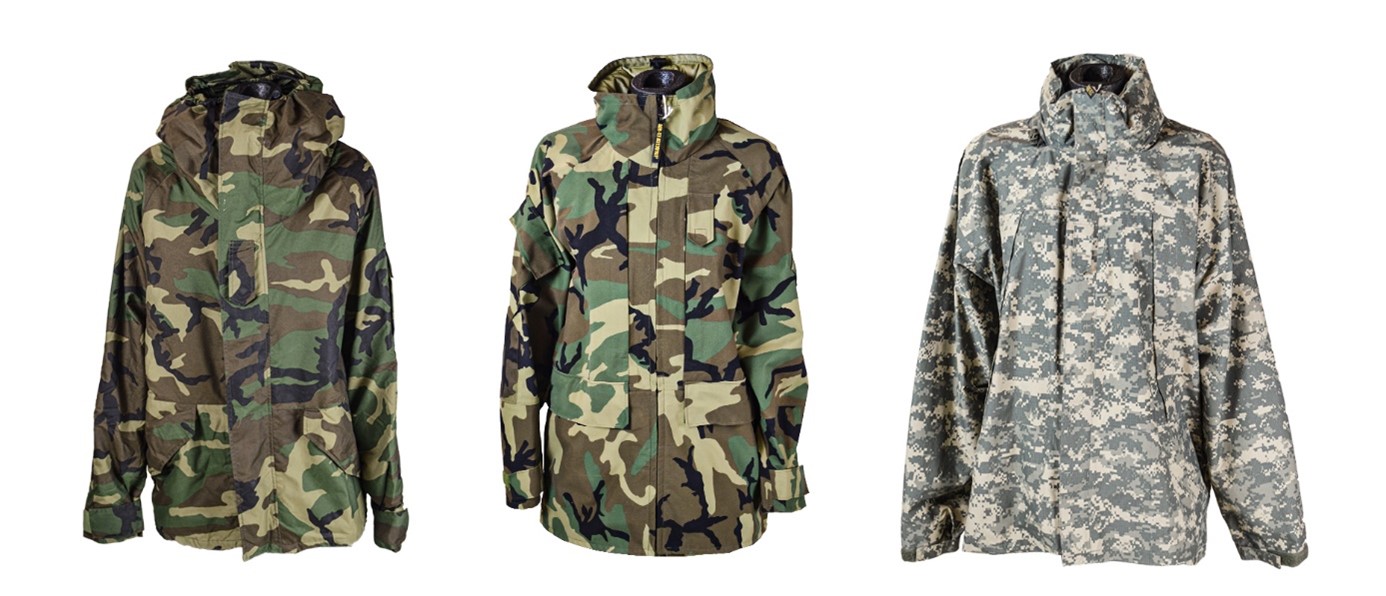
Figure 6: History of ECWCS Gen 1, 2 and 3. Source: Gore Heritage & Archive Collection.